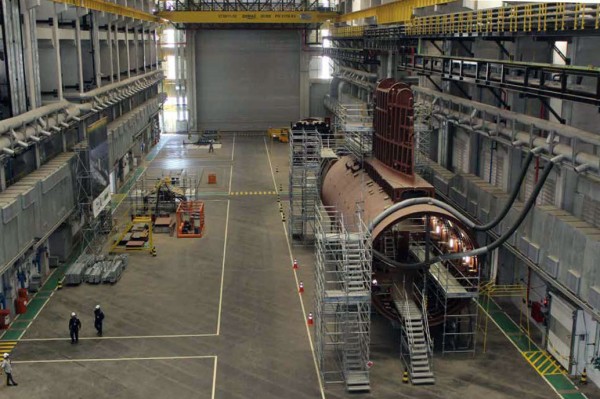
Neste período, o programa incluiu a qualificação de profissionais brasileiros nas instalações da DCNS na França, em serviços como soldagem, conformação de peças e fabricação de estrutura, e também, o treinamento ‘on the job training’ com a participação do pessoal na construção das duas seções ali executadas.
A partir de meados de 2013, com inauguração e início de operação da Unidade de Fabricação de Estruturas Metálicas (UFEM) em Itaguaí-RJ, a chegada das seções 3 e 4 ao Brasil e o retorno ao país, dos profissionais qualificados na França, a Marinha pôde imprimir uma dinâmica maior ao ritmo de construção do SBR-1.
A implantação de outra linha de produção na NUCLEP, direcionada a fabricação de anéis de reforço do submarino, que inclusive, constitui uma parte crítica no prazo de execução do casco resistente das embarcações, além de ampliar a capacidade de produção das seções do SBR-1, permitiu à Marinha iniciar a fabricação do segundo submarino convencional da série, o SBR-2.
“Realizamos os ajustes necessários para a operação da UFEM, que constituem parte do processo de partida de qualquer unidade fabril com o porte e a complexidade da UFEM, envolvendo equipamentos e softwares sofisticados e interface com diversos sistemas, e, hoje, a produção desta unidade é uma realidade. Na NUCLEP, ampliamos a produtividade da empresa, com uma segunda linha de montagem, para que pudéssemos garantir o atendimento ao cronograma do Prosub”, expõe Contra-Almirante Sydney dos Santos Neves, Gerente do empreendimento modular de obtenção dos submarinos convencionais da Coordenadoria-Geral do Programa de Desenvolvimento de Submarino com Propulsão Nuclear (COGESN).
Paralelamente à construção e à organização de toda a estrutura fabril em Itaguaí e à qualificação do pessoal na França – militares e civis da Marinha, da NUCLEP, da ICN e de outras empresas -, a Marinha e a DCNS iniciaram o processo de seleção de empresas fornecedoras para os submarinos do Prosub, adotando neste campo, uma das principais diretrizes do programa: a nacionalização de sistemas e de equipamentos.
Além de promover o estabelecimento de um parque industrial nacional com capacidade de desenvolver e fabricar equipamentos e componentes para todos os cinco submarinos, o programa de nacionalização do Prosub visa estabelecer uma base industrial e comercial no País de modo a assegurar a continuidade e a operação do projeto nos prazos e custos previstos.
Para os submarinos convencionais, 102 empresas já estão pré-qualificadas pela DCNS e, várias destas, já foram submetidas à aprovação da Marinha.
O programa de nacionalização dos submarinos convencionais inclui mais de 90 projetos prioritários direcionados ao fornecimento de itens como, ventiladores; conversores estáticos; mancais de escora; trocadores de calor; válvulas; sistemas eletrônicos; geradores; motores elétricos; sistema de combate; acumuladores hidráulicos, e outros. Entre os projetos já aprovados e/ou executados estão:
1. Engenharia e Integração do Sistema de Combate
O Sistema de Combate (SC) no submarino tem a função de gerenciar os sistemas de detecção (sonar, radar, navegação e periscópio) e calcular a solução de tiro para lançamento dos torpedos.
A Fundação Atech, hoje denominada Fundação Ezute, foi selecionada e aprovada para receber o treinamento e participar do desenvolvimento de módulos de software do SC.
No período compreendido entre setembro de 2011 a abril de 2015, oito engenheiros da Fundação Ezute estarão nas dependências da DCNS, na cidade de Toulon – França, recebendo treinamento referente aos módulos de software do SC dos S-BR. Nos anos de 2015 a 2017, a Ezute participará no Brasil, das atividades de integração do Sistema de Combate para o primeiro S-BR; e, após a conclusão do projeto, a Fundação será responsável pela manutenção do Sistema de Combate dos quatro submarinos convencionais.
2. Sistema de gerenciamento integrado da plataforma – IPMS
O IPMS é um sistema computacional responsável pelo controle de diversas funções no submarino, tais como, controle de navegação, profundidade, propulsão, qualidade de vida e segurança a bordo, energia elétrica, entre outros.
A Mectron, sediada em São José dos Campos – SP, é a empresa selecionada pela DCNS e Marinha para participar do desenvolvimento do IPMS dos submarinos. O processo de nacionalização incluiu o treinamento, na França, de engenheiros da empresa e oficiais da MB, os quais, inclusive, já retornaram ao Brasil.
3. Mancais de escora
O objetivo da nacionalização neste projeto é envolver uma empresa brasileira na produção e montagem completa do mancal de escora de acordo com os desenhos, requisitos e projeto da DCNS. Em um submarino, o mancal de escora tem a função de transferir o torque do motor elétrico para o hélice.
A Zollern, localizada em Cataguases – MG foi a empresa selecionada pela DCNS e aprovada pela MB para a fabricação dos mancais de escora. Inicialmente, a previsão deste projeto seria produzir o primeiro mancal (para o S-BR1) na França, como treinamento, e os outros três, no Brasil.
Como fruto da negociação entre a empresa brasileira e a DCNS, houve um aumento do escopo inicial do projeto, no qual ocorreu a substituição de treinamento para o primeiro mancal na França, pela fabricação de todos os mancais na Zollern. Soma-se ainda, a construção de um equipamento de testes dos mancais de escora pela Zollern com participação da UNESP (Universidade Estadual Paulista –Ilha Solteira-SP) e a supervisão da DCNS.
4. Tubos trocadores de calor
O objetivo deste projeto no Prosub é envolver, progressivamente, uma empresa brasileira, sob a responsabilidade da DCNS, na fabricação de componentes para trocadores de calor dos submarinos S-BR, produzidos de acordo com as especificações técnicas e a supervisão da DCNS.
A empresa selecionada pela DCNS e aprovada pela MB foi a Termomecânica, localizada em São Bernardo do Campo – SP, a qual já produziu, com sucesso, um lote de tubos de Cupro-Níquel que serão instalados nos trocadores de calor do sistema de resfriamento de baterias do S-BR.
5. Ventiladores
Os ventiladores dos S-BR, em total de três por submarino, tem por função a ventilação a bordo, em especial da praça de baterias, onde a manutenção do baixo teor de hidrogênio é essencial para as condições de habitabilidade da tripulação do submarino.
Este projeto visa o envolvimento de uma empresa brasileira no desenvolvimento, na qualificação e na produção dos ventiladores dos submarinos S-BR, de acordo com os requisitos e as especificações técnicas da DCNS.
A empresa escolhida pela DCNS e aprovada pela MB foi a Howden France, sua fornecedora na Europa. Através de um processo de Transferência de Tecnologia, a Howden France subcontratará a Howden South America, empresa brasileira localizada em Itatiba – SP, que será a responsável pela fabricação dos ventiladores.
6. Conversores estáticos
A função dos conversores estáticos é alimentar as redes elétricas do submarino. A Adelco, empresa brasileira sediada em Barueri – SP, foi selecionada pela DCNS e aprovada pela MB como responsável pelo desenvolvimento e fabricação dos conversores estáticos. Ao todo, serão 16 conversores, sendo quatro por submarino.
O contrato prevê a fabricação dos dois primeiros na França, com treinamento e transferência de tecnologia, e os 14 restantes, totalmente produzidos e fabricados no Brasil.
7. Motores elétricos
Os motores elétricos nos submarinos possuem várias aplicações a bordo. Neste projeto, a WEG Equipamentos, empresa brasileira sediada em Jaraguá do Sul – SC, foi selecionada pela DCNS e aprovada pela MB, para fabricar os motores destinados aos submarinos convencionais do Prosub.
8. Bateria
Neste caso, a bateria do SBR-1, será feita na Alemanha, na empresa Hagen, do grupo Exide, e, paulatinamente, a fabricação será realizada no Brasil: 30% para o SBR-2; 60% para o SBR-3; e 100% para o SBR-4. Neste processo, a transferência de tecnologia envolve o grupo Exide e a empresa Rondopar, com sede em Londrina – PR.
O processo de nacionalização de sistemas, equipamentos e componentes dos submarinos, além do treinamento para o desenvolvimento e a integração de softwares específicos, inclui, também, a fabricação dos itens e o suporte técnico para as empresas durante a fabricação. Segundo Almirante Neves, “o programa de nacionalização dos submarinos visa o fornecimento à série dos convencionais, e como evolução deste processo, a obtenção de uma capacidade fabril nacional para o submarino com propulsão nuclear. Pretendemos que as empresas nesta etapa do programa estejam capacitadas e aptas a atender, em suas respectivas áreas, as necessidades do submarino com propulsão nuclear”.
O Almirante Neves acrescenta ainda que, no âmbito da qualidade, a inspeção da DCNS é rigorosa e acompanha todas as etapas de fabricação dos itens executados no Brasil. A rastreabilidade, segundo o Almirante, é outro ponto de grande relevância na construção dos submarinos.
“Todos os equipamentos e sistemas considerados vitais são detalhadamente documentados, de forma que estes registros possam, no futuro, possibilitar o rastreamento de fabricação de cada item do submarino.”
FONTE: Technonews