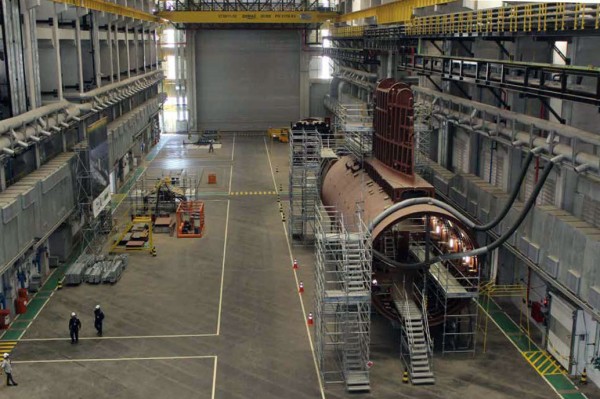
A construção do primeiro submarino do Prosub (o SBR-1) teve início em 2010, com a fabricação de seções de vante 3 e 4 na França, e as demais seções do casco, nas instalações da Nuclep no Brasil.
Neste período, o programa incluiu a qualificação de profissionais brasileiros nas instalações da DCNS na França, em serviços como soldagem, conformação de peças e fabricação de estrutura, e também, o treinamento ‘on the job training’ com a participação do pessoal na construção das duas seções ali executadas.
A partir de meados de 2013, com inauguração e início de operação da Unidade de Fabricação de Estruturas Metálicas (UFEM) em Itaguaí-RJ, a chegada das seções 3 e 4 ao Brasil e o retorno ao país, dos profissionais qualificados na França, a Marinha pôde imprimir uma dinâmica maior ao ritmo de construção do SBR-1.
A implantação de outra linha de produção na NUCLEP, direcionada a fabricação de anéis de reforço do submarino, que inclusive, constitui uma parte crítica no prazo de execução do casco resistente das embarcações, além de ampliar a capacidade de produção das seções do SBR-1, permitiu à Marinha iniciar a fabricação do segundo submarino convencional da série, o SBR-2.
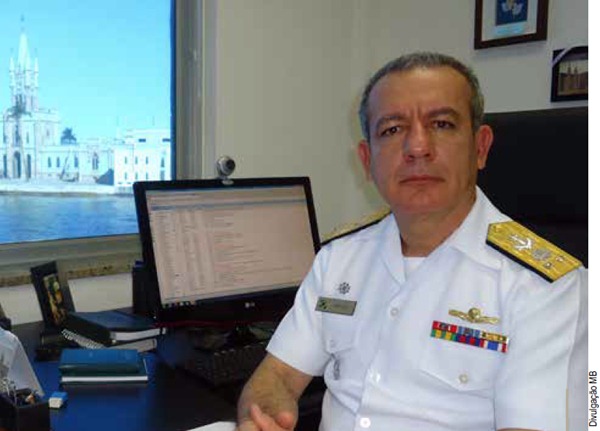
“Realizamos os ajustes necessários para a operação da UFEM, que constituem parte do processo de partida de qualquer unidade fabril com o porte e a complexidade da UFEM, envolvendo equipamentos e softwares sofisticados e interface com diversos sistemas, e, hoje, a produção desta unidade é uma realidade. Na NUCLEP, ampliamos a produtividade da empresa, com uma segunda linha de montagem, para que pudéssemos garantir o atendimento ao cronograma do Prosub”, expõe Contra-Almirante Sydney dos Santos Neves, Gerente do empreendimento modular de obtenção dos submarinos convencionais da Coordenadoria-Geral do Programa de Desenvolvimento de Submarino com Propulsão Nuclear (COGESN).
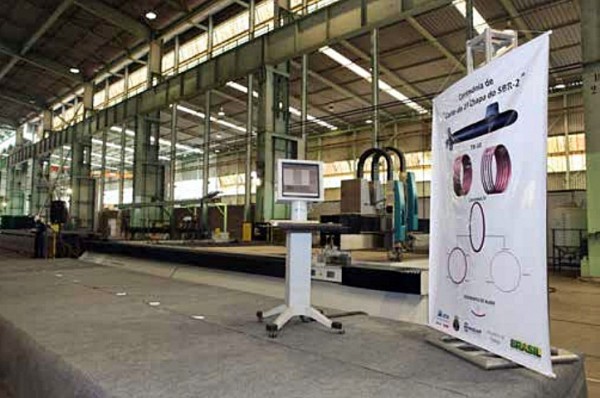
Paralelamente à construção e à organização de toda a estrutura fabril em Itaguaí e à qualificação do pessoal na França – militares e civis da Marinha, da NUCLEP, da ICN e de outras empresas -, a Marinha e a DCNS iniciaram o processo de seleção de empresas fornecedoras para os submarinos do Prosub, adotando neste campo, uma das principais diretrizes do programa: a nacionalização de sistemas e de equipamentos.
Além de promover o estabelecimento de um parque industrial nacional com capacidade de desenvolver e fabricar equipamentos e componentes para todos os cinco submarinos, o programa de nacionalização do Prosub visa estabelecer uma base industrial e comercial no País de modo a assegurar a continuidade e a operação do projeto nos prazos e custos previstos.
Para os submarinos convencionais, 102 empresas já estão pré-qualificadas pela DCNS e, várias destas, já foram submetidas à aprovação da Marinha.
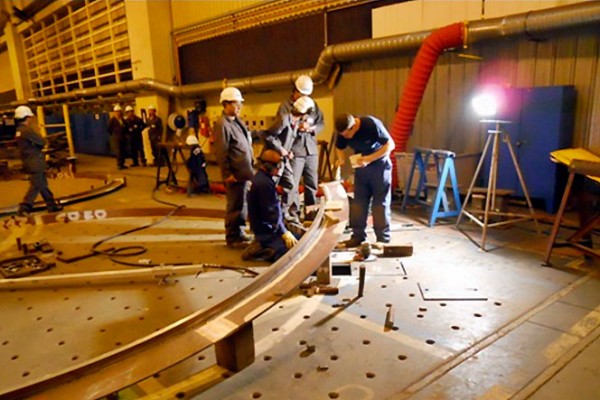
O programa de nacionalização dos submarinos convencionais inclui mais de 90 projetos prioritários direcionados ao fornecimento de itens como, ventiladores; conversores estáticos; mancais de escora; trocadores de calor; válvulas; sistemas eletrônicos; geradores; motores elétricos; sistema de combate; acumuladores hidráulicos, e outros. Entre os projetos já aprovados e/ou executados estão:
1. Engenharia e Integração do Sistema de Combate
O Sistema de Combate (SC) no submarino tem a função de gerenciar os sistemas de detecção (sonar, radar, navegação e periscópio) e calcular a solução de tiro para lançamento dos torpedos.
A Fundação Atech, hoje denominada Fundação Ezute, foi selecionada e aprovada para receber o treinamento e participar do desenvolvimento de módulos de software do SC.
No período compreendido entre setembro de 2011 a abril de 2015, oito engenheiros da Fundação Ezute estarão nas dependências da DCNS, na cidade de Toulon – França, recebendo treinamento referente aos módulos de software do SC dos S-BR. Nos anos de 2015 a 2017, a Ezute participará no Brasil, das atividades de integração do Sistema de Combate para o primeiro S-BR; e, após a conclusão do projeto, a Fundação será responsável pela manutenção do Sistema de Combate dos quatro submarinos convencionais.
2. Sistema de gerenciamento integrado da plataforma – IPMS
O IPMS é um sistema computacional responsável pelo controle de diversas funções no submarino, tais como, controle de navegação, profundidade, propulsão, qualidade de vida e segurança a bordo, energia elétrica, entre outros.
A Mectron, sediada em São José dos Campos – SP, é a empresa selecionada pela DCNS e Marinha para participar do desenvolvimento do IPMS dos submarinos. O processo de nacionalização incluiu o treinamento, na França, de engenheiros da empresa e oficiais da MB, os quais, inclusive, já retornaram ao Brasil.
3. Mancais de escora
O objetivo da nacionalização neste projeto é envolver uma empresa brasileira na produção e montagem completa do mancal de escora de acordo com os desenhos, requisitos e projeto da DCNS. Em um submarino, o mancal de escora tem a função de transferir o torque do motor elétrico para o hélice.
A Zollern, localizada em Cataguases – MG foi a empresa selecionada pela DCNS e aprovada pela MB para a fabricação dos mancais de escora. Inicialmente, a previsão deste projeto seria produzir o primeiro mancal (para o S-BR1) na França, como treinamento, e os outros três, no Brasil.
Como fruto da negociação entre a empresa brasileira e a DCNS, houve um aumento do escopo inicial do projeto, no qual ocorreu a substituição de treinamento para o primeiro mancal na França, pela fabricação de todos os mancais na Zollern. Soma-se ainda, a construção de um equipamento de testes dos mancais de escora pela Zollern com participação da UNESP (Universidade Estadual Paulista –Ilha Solteira-SP) e a supervisão da DCNS.
4. Tubos trocadores de calor
O objetivo deste projeto no Prosub é envolver, progressivamente, uma empresa brasileira, sob a responsabilidade da DCNS, na fabricação de componentes para trocadores de calor dos submarinos S-BR, produzidos de acordo com as especificações técnicas e a supervisão da DCNS.
A empresa selecionada pela DCNS e aprovada pela MB foi a Termomecânica, localizada em São Bernardo do Campo – SP, a qual já produziu, com sucesso, um lote de tubos de Cupro-Níquel que serão instalados nos trocadores de calor do sistema de resfriamento de baterias do S-BR.
5. Ventiladores
Os ventiladores dos S-BR, em total de três por submarino, tem por função a ventilação a bordo, em especial da praça de baterias, onde a manutenção do baixo teor de hidrogênio é essencial para as condições de habitabilidade da tripulação do submarino.
Este projeto visa o envolvimento de uma empresa brasileira no desenvolvimento, na qualificação e na produção dos ventiladores dos submarinos S-BR, de acordo com os requisitos e as especificações técnicas da DCNS.
A empresa escolhida pela DCNS e aprovada pela MB foi a Howden France, sua fornecedora na Europa. Através de um processo de Transferência de Tecnologia, a Howden France subcontratará a Howden South America, empresa brasileira localizada em Itatiba – SP, que será a responsável pela fabricação dos ventiladores.
6. Conversores estáticos
A função dos conversores estáticos é alimentar as redes elétricas do submarino. A Adelco, empresa brasileira sediada em Barueri – SP, foi selecionada pela DCNS e aprovada pela MB como responsável pelo desenvolvimento e fabricação dos conversores estáticos. Ao todo, serão 16 conversores, sendo quatro por submarino.
O contrato prevê a fabricação dos dois primeiros na França, com treinamento e transferência de tecnologia, e os 14 restantes, totalmente produzidos e fabricados no Brasil.
7. Motores elétricos
Os motores elétricos nos submarinos possuem várias aplicações a bordo. Neste projeto, a WEG Equipamentos, empresa brasileira sediada em Jaraguá do Sul – SC, foi selecionada pela DCNS e aprovada pela MB, para fabricar os motores destinados aos submarinos convencionais do Prosub.
8. Bateria
Neste caso, a bateria do SBR-1, será feita na Alemanha, na empresa Hagen, do grupo Exide, e, paulatinamente, a fabricação será realizada no Brasil: 30% para o SBR-2; 60% para o SBR-3; e 100% para o SBR-4. Neste processo, a transferência de tecnologia envolve o grupo Exide e a empresa Rondopar, com sede em Londrina – PR.
O processo de nacionalização de sistemas, equipamentos e componentes dos submarinos, além do treinamento para o desenvolvimento e a integração de softwares específicos, inclui, também, a fabricação dos itens e o suporte técnico para as empresas durante a fabricação. Segundo Almirante Neves, “o programa de nacionalização dos submarinos visa o fornecimento à série dos convencionais, e como evolução deste processo, a obtenção de uma capacidade fabril nacional para o submarino com propulsão nuclear. Pretendemos que as empresas nesta etapa do programa estejam capacitadas e aptas a atender, em suas respectivas áreas, as necessidades do submarino com propulsão nuclear”.
O Almirante Neves acrescenta ainda que, no âmbito da qualidade, a inspeção da DCNS é rigorosa e acompanha todas as etapas de fabricação dos itens executados no Brasil. A rastreabilidade, segundo o Almirante, é outro ponto de grande relevância na construção dos submarinos.
“Todos os equipamentos e sistemas considerados vitais são detalhadamente documentados, de forma que estes registros possam, no futuro, possibilitar o rastreamento de fabricação de cada item do submarino.”
FONTE: Technonews
mas sempre tem os do contra que tentam atrapalhar o projeto mas a coisa anda e felicidade vem chegando com o sub nuclear
Oui,oui,oui Monsieur sem duvida este programa é importante p nosso bem ,estar avançando e sem dúvida nenhuma o + importante 95% do comerçio riquezas deste pais passam pelo mar .era pra ontem kkkkkkk + esta se tornando realidade
Os conversores estáticos que a ADELCO irá fornecer tem um papel importantíssimo de retificar a senóide dos geradores de tensão alternada (VCA) e transformar em tensão contínua (VCC) e fornecer a carga para o banco de baterias que só pode ser alimentado com VCC (é como um carregador de baterias, na tomada de casa temos VCA, ele retifica para VCC e alimenta as baterias, nos submarinos é a mesma coisa) que por sua vez alimenta o painel de controle do motor de corrente contínua que será produzido pela WEG.
Por fim o motor está diretamente acoplado ao hélice e conta com um sistema de controle da tensão aplicada sobre ele para se ter um ótimo controle de velocidade de 0 a 100 %.
Outra coisa que achei interessante no esquema de propulsão do nosso submarino nuclear é que a água condensada do vapor que impulsiona os turbo geradores será bombada de volta para a geração de vapor num circuito fechado, claro independentemente do circuito de água leve pressurizada usado no arrefecimento do reator.
Todo esse processo entre muitos outros será gerenciado pelo sistema IPMS que ficou a cargo da MECTRON desenvolver.
E oque vemos quando se fala isso? Tecnologia, muita, muita tecnologia, e tecnologia muito sensível. Isso sim é transferência de tecnologia!
Esse projeto está indo de vento e poupa enquanto os outros que são importantes nem DEUS sabe quando vão sair.
Mauricio, o importante é que, o projeto mais complexo e o de maior agregado tecnológico que é o PROSUB , está evoluindo , conforme previsto. Quanto aos demais projetos da MB, estes virão a seu tempo.
Você quis dizer popa?
Sensacional esse trabalho. Pode ter gerado críticas de muito mas ao meu ver, é um desenvolvimento vibrante para a indústria naval bélica brasileira. Sem contar que do lado portenho deve estar gerando uma inveja gigantesca. Tudo bem que eles já não servem de referência no assunto mas azar no futebol sorte na indústria.